Plures Intelligens Modicum Machinatorem
808 Gilman Street Berkeley, CA 94710 | 510-549-3300 | admin@bearinc.com
Dr. Glen Stevick, P.E. ext. 101 | Dr. Dave Rondinone, P.E. ext. 102 | Derek King, P.E. ext. 103 | Mingxi Zheng, P.E. ext. 106
Risk Management.
Any pipeline rupture is an example of failure in risk management. Many BEAR engineers are in the ASME Piping Code Mechanical Design Committee and have performed the fracture assessment of the Alaska Pipeline, continually analyzing the strength and structural integrity of all types of pipes materials.
testing pipe integrity
BEAR engineers have the ability to set up unique tests to assess pipes in both normal and unusual operating conditions. The photograph below (left) shows a fatigue test machine, which BEAR engineers built specifically to test refinery piping elbows with thin spots. The video below (right) shows a high pressure burst test conducted at BEAR to determine the pressure resistance of large diameter gas pipe with the consideration of thinning due to corrosion and a longitudinal weld only halfway through the pipe wall thickness.
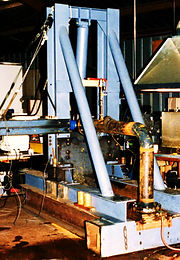
Documenting BEAR's Testing
risk analysis process
When pipeline is examined for the potential of the risk of failure, BEAR engineers use the risk modeling which is described below. Risk analysis typically starts with researching for similarities in past cases and moves to a design re-appraisal. Afterwards, BEAR engineers assess the individual key operating factors and possible damage events by performing data collection and inspection.
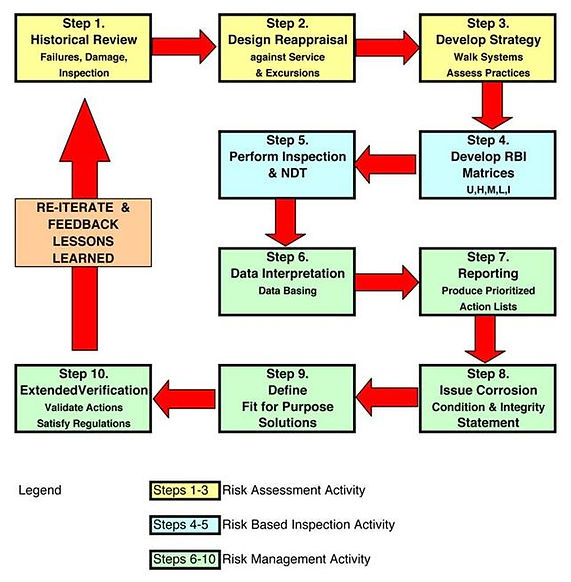
The graph below shows the general risk failure rate of pipelines as a function of time, often referred to as a "bathtub" curve. Failures and problems are high at first, but later, construction defects are eliminated. Then, there is a long period with few problems that typically lasts many decades. This is followed by an increase in failures as the pipeline nears the end of its life. However, when a third party intervenes, the lifetime of the pipeline will have a higher rate of field failures. According to the graph, even during the "useful life" period, the failure rate is as high as during the "early life" period.

damage mechanism to inspection method relationship
Damage Mechanism
Weld Fatigue, Incomplete Welding, and Cracking
Corrosion
Third Party Damage, i.e. backhoe strikes and solid movement especially with older pipes
Inspection/Detection Methods
Hydrostatic pressure test
Pigging, Direct inspection, Hydrostatic pressure test
Hydrostatic pressure test
Note: only hydrostatic pressure testing can be used to detect and mitigate all common damage mechanisms.